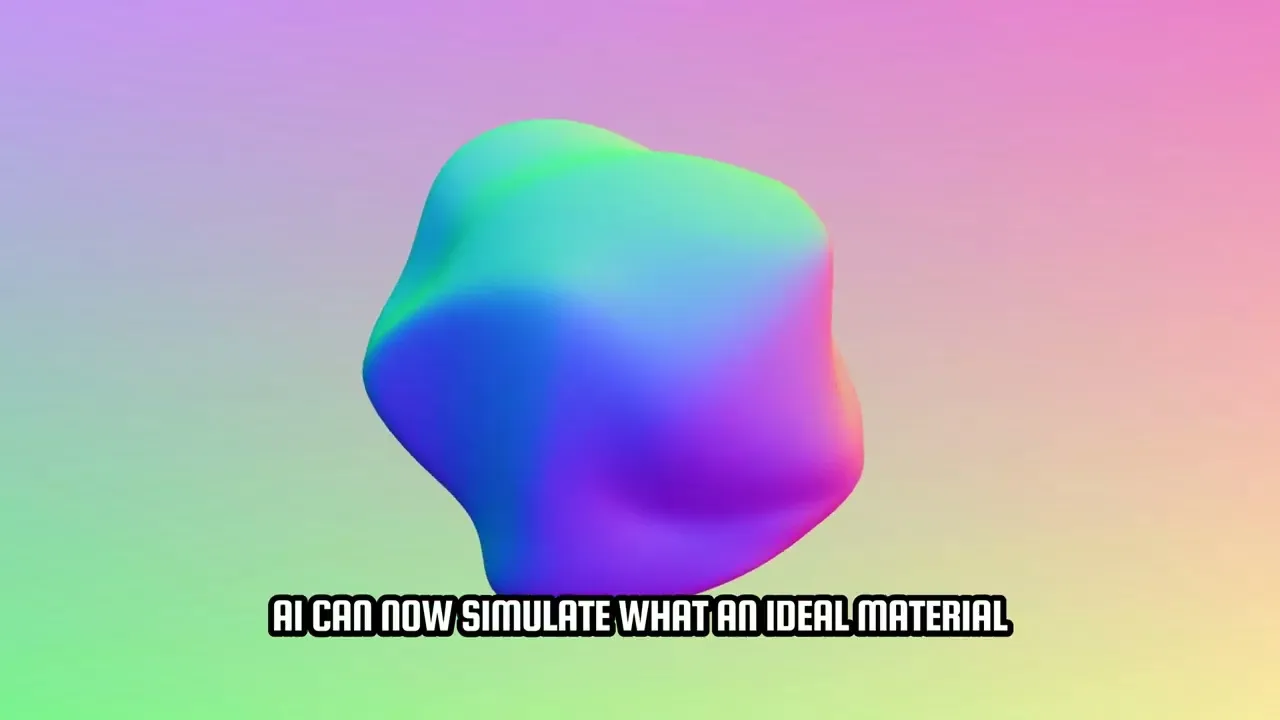
Materials
Data Factory
Fueling AI with
Materials x Manufacturing data
Fueling AI with
Materials x Manufacturing data
Read more:
Read more:
Read more:
AI dreams up the material. We manufacture it
Models trained on our experimental data unlock step-by-step synthesis planning
—the bottleneck that keeps materials from ever leaving simulations or the lab.
We enable AI to build
the materials it dreams up
Models trained on our experimental datasets unlock step-by-step synthesis planning
—the bottleneck that keeps materials from ever leaving simulations or the lab.
We enable AI to manufacture
the materials it dreams up
Models trained on our experimental datasets unlock step-by-step synthesis planning
—the bottleneck that keeps materials from ever leaving simulations or the lab.
AI dreams up the material. We manufacture it
Models trained on our experimental data unlock step-by-step synthesis planning
—the bottleneck that keeps materials from ever leaving simulations or the lab.
AI dreams up the material. We manufacture it
Models trained on our experimental data unlock step-by-step synthesis planning
—the bottleneck that keeps materials from ever leaving simulations or the lab.
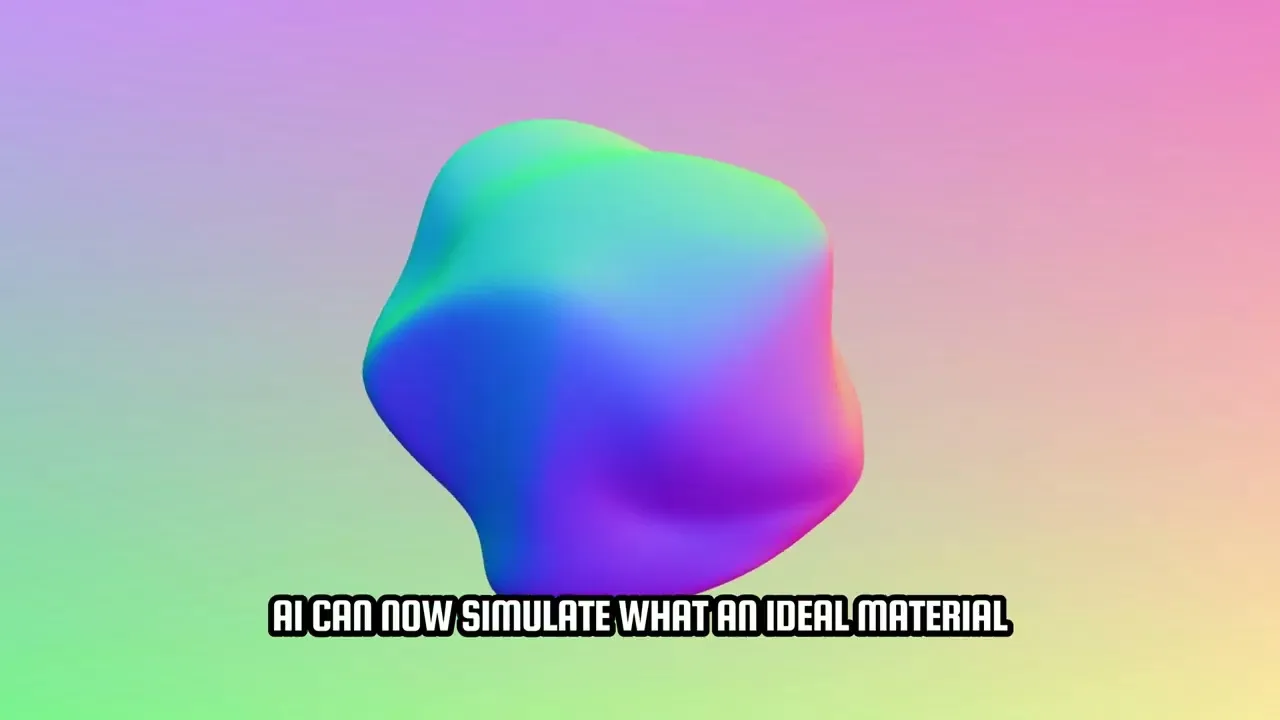
With our physical data, AI goes from theory to impact.
Here’s what it can do
With our physical data, AI goes from theory to impact. Here’s what it can do
With our physical data, AI goes from theory to impact.Here’s what it can do
Unlock transformative leaps in technology
Tackle the world’s toughest challenges—greenhouse gas capture and removal, decarbonization, clean water access, and environment remediation. It can be a force multiplier for science that truly serves humanity.

Unlock transformative leaps in tech
Tackle the world’s toughest challenges—greenhouse gas capture and removal, decarbonization, clean water access, and environment remediation. It can be a force multiplier for science that truly serves humanity.

Unlock transformative leaps in technology
Tackle the world’s toughest challenges—greenhouse gas capture and removal, decarbonization, clean water access, and environment remediation. It can be a force multiplier for science that truly serves humanity.

Unlock transformative leaps in technology
Tackle the world’s toughest challenges—greenhouse gas capture and removal, decarbonization, clean water access, and environment remediation. It can be a force multiplier for science that truly serves humanity.

Democratize materials innovation
With just a GPU, researchers and startups without lab access could evaluate the manufacturing of new materials—lowering the barrier to entry and enabling product innovation from small teams or niche ideas and markets.

Democratize materials innovation
With just a GPU, researchers and startups without lab access could evaluate the manufacturing of new materials—lowering the barrier to entry and enabling product innovation from small teams or niche ideas and markets.

Democratize materials innovation
With just a GPU, researchers and startups without lab access could evaluate the manufacturing of new materials—lowering the barrier to entry and enabling product innovation from small teams or niche ideas and markets.

Democratize materials innovation
With just a GPU, researchers and startups without lab access could evaluate the manufacturing of new materials—lowering the barrier to entry and enabling product innovation from small teams or niche ideas and markets.

De-risk early materials R&D
Assess whether a material could be manufactured—before entering the lab—saving time, cost, and reducing risk in early R&D. This bridges early research and industry, giving teams the confidence to explore new materials with a realistic view of scale-up feasibility.

De-risk early materials R&D
Assess whether a material could be manufactured—before entering the lab—saving time, cost, and reducing risk in early R&D. This bridges early research and industry, giving teams the confidence to explore new materials with a realistic view of scale-up feasibility.

De-risk early materials R&D
Assess whether a material could be manufactured—before entering the lab—saving time, cost, and reducing risk in early R&D. This bridges early research and industry, giving teams the confidence to explore new materials with a realistic view of scale-up feasibility.

De-risk early materials R&D
Assess whether a material could be manufactured—before entering the lab—saving time, cost, and reducing risk in early R&D. This bridges early research and industry, giving teams the confidence to explore new materials with a realistic view of scale-up feasibility.

Scale up using existing infrastructure
Identify materials that could be manufactured at scale using current infrastructure and supply chains—avoiding costly and long process changes.

Scale up using existing infrastructure
Identify materials that could be manufactured at scale using current infrastructure and supply chains—avoiding costly and long process changes.

Scale up using existing infrastructure
Identify materials that could be manufactured at scale using current infrastructure and supply chains—avoiding costly and long process changes.

Scale up using existing infrastructure
Identify materials that could be manufactured at scale using current infrastructure and supply chains—avoiding costly and long process changes.

Break down silos across industries
Offer a a common reference for assessing materials manufacturability — improving reproducibility and making it easier to translate findings across teams, companies, and even industries.

Break down silos across industries
Offer a a common reference for assessing materials manufacturability — improving reproducibility and making it easier to translate findings across teams, companies, and even industries.

Break down silos across industries
Offer a a common reference for assessing materials manufacturability — improving reproducibility and making it easier to translate findings across teams, companies, and even industries.

Break down silos across industries
Offer a a common reference for assessing materials manufacturability — improving reproducibility and making it easier to translate findings across teams, companies, and even industries.

Build one engine for many frontiers
Not built for one-off tasks—our datasets will be designed to be adaptable. As needs evolve, the same data can be re-utilized to unlock breakthroughs in new applications—maximizing impact and return on investment.

Build one engine for many frontiers
Not built for one-off tasks—our datasets will be designed to be adaptable. As needs evolve, the same data can be re-utilized to unlock breakthroughs in new applications—maximizing impact and return on investment.

Build one engine for many frontiers
Not built for one-off tasks—our datasets will be designed to be adaptable. As needs evolve, the same data can be re-utilized to unlock breakthroughs in new applications—maximizing impact and return on investment.

Build one engine for many frontiers
Not built for one-off tasks—our datasets will be designed to be adaptable. As needs evolve, the same data can be re-utilized to unlock breakthroughs in new applications—maximizing impact and return on investment.

What & Why
What & Why
What & Why
Applications
Here's a glimpse into some of the most pressing challenges we’re ready to tackle first
Here's a glimpse into some of the most pressing challenges we’re ready to tackle first
Here's a glimpse into some of the most pressing challenges we’re ready to tackle first

Carbon Capture
To meet net-zero targets, the world needs to remove 10 billion tons of CO₂ annually by 2050. MOFs are porous crystalline materials that can selectively adsorb CO₂ at low concentrations and release it using far less energy than amine solvents. They can be tuned to work under various capture conditions and regenerate with low-temperature heat or vacuum. This makes them ideal for a wide range of capture applications—from direct air capture (DAC) to point-source capture in cement, steel, and chemical plants. But to deliver this impact, MOFs must be designed for high uptake, low regeneration energy, long-term durability, and scalable, low-cost manufacturing. By unlocking the ability to rapidly and cost-effectively manufacture the right MOFs, we can dramatically reduce the cost of CO₂ capture—bringing it in line with the U.S. DOE targets of $30/ton for point sources and $100/ton for DAC.
Used Tools
Figma
Framer
Lottie
Build to Launch
7 weeks
01

Water Harvesting
To ensure a healthy and equitable future, the world must secure reliable access to clean water—an increasingly urgent challenge as climate change, pollution, and population growth strain existing supplies. Emerging materials like MOFs can transform how we harvest water, making it possible to extract moisture from air. But to scale these solutions, materials must be engineered for high selectivity, low energy use, and long-term resilience in diverse environments. By advancing water harvesting we can bring safe drinking water to the 2 billion people who currently lack it—while building climate resilience for the future.
Used Tools
Figma
Framer
Lottie
Build to Launch
7 weeks
02

Green fuels and chemicals
What if we could clean up the dirtiest parts of industry—like making steel, flying planes, producing fertilizer, or creating everyday chemicals? These sectors produce over 20% of global CO₂ emissions and rely heavily on fossil fuel feedstocks making them the hardest to clean up. By driving chemical reactions with renewable electricity (electro-chemical reactions), we can (1) make hydrogen from water and (2) turn the world’s biggest waste–CO₂– into green building blocks for cleaner hydrocarbons. This opens the door to reimagining the future of the petrochemical industry without fossil fuels. Meeting projected demand for green hydrogen and related technologies would require over 2,000 tons of Iridium annually by 2050—more than 200 times today’s supply. Without new ways to reduce Iridium use, recycle it more efficiently, or replace it with abundant alternatives, we simply can’t scale the clean technologies needed to decarbonize heavy industry and transport.
Used Tools
Figma
Framer
Lottie
Build to Launch
7 weeks
03

Early Disease Diagnosis
New sensor technologies, inspired by the biological olfactory systems of living organisms are emerging as a powerful tool for health diagnostics. These devices use sensor arrays to detect and analyze volatile organic compounds (VOCs) in breath or bodily fluids, enabling non-invasive, real-time detection of disease biomarkers. Their core functionality relies on sensing materials that transduce chemical signals into electrical data—materials such as chemiresistors, conductive polymers, optical sensors, surface acoustic wave devices, and electrochemical sensors. Advances in these materials open the door to portable, low-cost diagnostic tools capable of detecting early-stage illnesses, offering new opportunities in personalized and preventive healthcare.
Used Tools
Figma
Framer
Lottie
Build to Launch
7 weeks
04

Carbon Capture
To meet net-zero targets, the world needs to remove 10 billion tons of CO₂ annually by 2050. MOFs are porous crystalline materials that can selectively adsorb CO₂ at low concentrations and release it using far less energy than amine solvents. They can be tuned to work under various capture conditions and regenerate with low-temperature heat or vacuum. This makes them ideal for a wide range of capture applications—from direct air capture (DAC) to point-source capture in cement, steel, and chemical plants. But to deliver this impact, MOFs must be designed for high uptake, low regeneration energy, long-term durability, and scalable, low-cost manufacturing. By unlocking the ability to rapidly and cost-effectively manufacture the right MOFs, we can dramatically reduce the cost of CO₂ capture—bringing it in line with the U.S. DOE targets of $30/ton for point sources and $100/ton for DAC.
Used Tools
Figma
Framer
Lottie
Build to Launch
7 weeks
01

Water Harvesting
To ensure a healthy and equitable future, the world must secure reliable access to clean water—an increasingly urgent challenge as climate change, pollution, and population growth strain existing supplies. Emerging materials like MOFs can transform how we harvest water, making it possible to extract moisture from air. But to scale these solutions, materials must be engineered for high selectivity, low energy use, and long-term resilience in diverse environments. By advancing water harvesting we can bring safe drinking water to the 2 billion people who currently lack it—while building climate resilience for the future.
Used Tools
Figma
Framer
Lottie
Build to Launch
7 weeks
02

Green fuels and chemicals
What if we could clean up the dirtiest parts of industry—like making steel, flying planes, producing fertilizer, or creating everyday chemicals? These sectors produce over 20% of global CO₂ emissions and rely heavily on fossil fuel feedstocks making them the hardest to clean up. By driving chemical reactions with renewable electricity (electro-chemical reactions), we can (1) make hydrogen from water and (2) turn the world’s biggest waste–CO₂– into green building blocks for cleaner hydrocarbons. This opens the door to reimagining the future of the petrochemical industry without fossil fuels. Meeting projected demand for green hydrogen and related technologies would require over 2,000 tons of Iridium annually by 2050—more than 200 times today’s supply. Without new ways to reduce Iridium use, recycle it more efficiently, or replace it with abundant alternatives, we simply can’t scale the clean technologies needed to decarbonize heavy industry and transport.
Used Tools
Figma
Framer
Lottie
Build to Launch
7 weeks
03

Early Disease Diagnosis
New sensor technologies, inspired by the biological olfactory systems of living organisms are emerging as a powerful tool for health diagnostics. These devices use sensor arrays to detect and analyze volatile organic compounds (VOCs) in breath or bodily fluids, enabling non-invasive, real-time detection of disease biomarkers. Their core functionality relies on sensing materials that transduce chemical signals into electrical data—materials such as chemiresistors, conductive polymers, optical sensors, surface acoustic wave devices, and electrochemical sensors. Advances in these materials open the door to portable, low-cost diagnostic tools capable of detecting early-stage illnesses, offering new opportunities in personalized and preventive healthcare.
Used Tools
Figma
Framer
Lottie
Build to Launch
7 weeks
04

Carbon Capture
To meet net-zero targets, the world needs to remove 10 billion tons of CO₂ annually by 2050. MOFs are porous crystalline materials that can selectively adsorb CO₂ at low concentrations and release it using far less energy than amine solvents. They can be tuned to work under various capture conditions and regenerate with low-temperature heat or vacuum. This makes them ideal for a wide range of capture applications—from direct air capture (DAC) to point-source capture in cement, steel, and chemical plants. But to deliver this impact, MOFs must be designed for high uptake, low regeneration energy, long-term durability, and scalable, low-cost manufacturing. By unlocking the ability to rapidly and cost-effectively manufacture the right MOFs, we can dramatically reduce the cost of CO₂ capture—bringing it in line with the U.S. DOE targets of $30/ton for point sources and $100/ton for DAC.
Used Tools
Figma
Framer
Lottie
Build to Launch
7 weeks
01

Water Harvesting
To ensure a healthy and equitable future, the world must secure reliable access to clean water—an increasingly urgent challenge as climate change, pollution, and population growth strain existing supplies. Emerging materials like MOFs can transform how we harvest water, making it possible to extract moisture from air. But to scale these solutions, materials must be engineered for high selectivity, low energy use, and long-term resilience in diverse environments. By advancing water harvesting we can bring safe drinking water to the 2 billion people who currently lack it—while building climate resilience for the future.
Used Tools
Figma
Framer
Lottie
Build to Launch
7 weeks
02

Green fuels and chemicals
What if we could clean up the dirtiest parts of industry—like making steel, flying planes, producing fertilizer, or creating everyday chemicals? These sectors produce over 20% of global CO₂ emissions and rely heavily on fossil fuel feedstocks making them the hardest to clean up. By driving chemical reactions with renewable electricity (electro-chemical reactions), we can (1) make hydrogen from water and (2) turn the world’s biggest waste–CO₂– into green building blocks for cleaner hydrocarbons. This opens the door to reimagining the future of the petrochemical industry without fossil fuels. Meeting projected demand for green hydrogen and related technologies would require over 2,000 tons of Iridium annually by 2050—more than 200 times today’s supply. Without new ways to reduce Iridium use, recycle it more efficiently, or replace it with abundant alternatives, we simply can’t scale the clean technologies needed to decarbonize heavy industry and transport.
Used Tools
Figma
Framer
Lottie
Build to Launch
7 weeks
03

Early Disease Diagnosis
New sensor technologies, inspired by the biological olfactory systems of living organisms are emerging as a powerful tool for health diagnostics. These devices use sensor arrays to detect and analyze volatile organic compounds (VOCs) in breath or bodily fluids, enabling non-invasive, real-time detection of disease biomarkers. Their core functionality relies on sensing materials that transduce chemical signals into electrical data—materials such as chemiresistors, conductive polymers, optical sensors, surface acoustic wave devices, and electrochemical sensors. Advances in these materials open the door to portable, low-cost diagnostic tools capable of detecting early-stage illnesses, offering new opportunities in personalized and preventive healthcare.
Used Tools
Figma
Framer
Lottie
Build to Launch
7 weeks
04
Applications
Here's a glimpse into some of the most pressing challenges we’re ready to tackle first

Carbon Capture
To meet net-zero targets, the world needs to remove 10 billion tons of CO₂ annually by 2050. MOFs are porous crystalline materials that can selectively adsorb CO₂ at low concentrations and release it using far less energy than amine solvents. They can be tuned to work under various capture conditions and regenerate with low-temperature heat or vacuum. This makes them ideal for a wide range of capture applications—from direct air capture (DAC) to point-source capture in cement, steel, and chemical plants. But to deliver this impact, MOFs must be designed for high uptake, low regeneration energy, long-term durability, and scalable, low-cost manufacturing. By unlocking the ability to rapidly and cost-effectively manufacture the right MOFs, we can dramatically reduce the cost of CO₂ capture—bringing it in line with the U.S. DOE targets of $30/ton for point sources and $100/ton for DAC.
Materials Class
Metal Organic Frameworks (MOFs)
01

Water Harvesting
To ensure a healthy and equitable future, the world must secure reliable access to clean water—an increasingly urgent challenge as climate change, pollution, and population growth strain existing supplies. Emerging materials like MOFs can transform how we harvest water, making it possible to extract moisture from air. But to scale these solutions, materials must be engineered for high selectivity, low energy use, and long-term resilience in diverse environments. By advancing water harvesting we can bring safe drinking water to the 2 billion people who currently lack it—while building climate resilience for the future.
Materials Class
Metal Organic Frameworks (MOFs)
02

Green fuels and chemicals
What if we could clean up the dirtiest parts of industry—like making steel, flying planes, producing fertilizer, or creating everyday chemicals? These sectors produce over 20% of global CO₂ emissions and rely heavily on fossil fuel feedstocks making them the hardest to clean up. By driving chemical reactions with renewable electricity (electro-chemical reactions), we can (1) make hydrogen from water and (2) turn the world’s biggest waste–CO₂– into green building blocks for cleaner hydrocarbons. This opens the door to reimagining the future of the petrochemical industry without fossil fuels. Meeting projected demand for green hydrogen and related technologies would require over 2,000 tons of Iridium annually by 2050—more than 200 times today’s supply. Without new ways to reduce Iridium use, recycle it more efficiently, or replace it with abundant alternatives, we simply can’t scale the clean technologies needed to decarbonize heavy industry and transport.
Materials Class
Alloys (Catalysts)
03

Early Disease Diagnosis
New sensor technologies, inspired by the biological olfactory systems of living organisms are emerging as a powerful tool for health diagnostics. These devices use sensor arrays to detect and analyze volatile organic compounds (VOCs) in breath or bodily fluids, enabling non-invasive, real-time detection of disease biomarkers. Their core functionality relies on sensing materials that transduce chemical signals into electrical data—materials such as chemiresistors, conductive polymers, optical sensors, surface acoustic wave devices, and electrochemical sensors. Advances in these materials open the door to portable, low-cost diagnostic tools capable of detecting early-stage illnesses, offering new opportunities in personalized and preventive healthcare.
Materials Class
Alloys (Oxides)
04
Applications
Here's a glimpse into some of the most pressing challenges we’re ready to tackle first

Carbon Capture
To meet net-zero targets, the world needs to remove 10 billion tons of CO₂ annually by 2050. MOFs are porous crystalline materials that can selectively adsorb CO₂ at low concentrations and release it using far less energy than amine solvents. They can be tuned to work under various capture conditions and regenerate with low-temperature heat or vacuum. This makes them ideal for a wide range of capture applications—from direct air capture (DAC) to point-source capture in cement, steel, and chemical plants. But to deliver this impact, MOFs must be designed for high uptake, low regeneration energy, long-term durability, and scalable, low-cost manufacturing. By unlocking the ability to rapidly and cost-effectively manufacture the right MOFs, we can dramatically reduce the cost of CO₂ capture—bringing it in line with the U.S. DOE targets of $30/ton for point sources and $100/ton for DAC.
Materials Class
Metal Organic Frameworks (MOFs)
01

Water Harvesting
To ensure a healthy and equitable future, the world must secure reliable access to clean water—an increasingly urgent challenge as climate change, pollution, and population growth strain existing supplies. Emerging materials like MOFs can transform how we harvest water, making it possible to extract moisture from air. But to scale these solutions, materials must be engineered for high selectivity, low energy use, and long-term resilience in diverse environments. By advancing water harvesting we can bring safe drinking water to the 2 billion people who currently lack it—while building climate resilience for the future.
Materials Class
Metal Organic Frameworks (MOFs)
02

Green fuels and chemicals
What if we could clean up the dirtiest parts of industry—like making steel, flying planes, producing fertilizer, or creating everyday chemicals? These sectors produce over 20% of global CO₂ emissions and rely heavily on fossil fuel feedstocks making them the hardest to clean up. By driving chemical reactions with renewable electricity (electro-chemical reactions), we can (1) make hydrogen from water and (2) turn the world’s biggest waste–CO₂– into green building blocks for cleaner hydrocarbons. This opens the door to reimagining the future of the petrochemical industry without fossil fuels. Meeting projected demand for green hydrogen and related technologies would require over 2,000 tons of Iridium annually by 2050—more than 200 times today’s supply. Without new ways to reduce Iridium use, recycle it more efficiently, or replace it with abundant alternatives, we simply can’t scale the clean technologies needed to decarbonize heavy industry and transport.
Materials Class
Alloys (Catalysts)
03

Early Disease Diagnosis
New sensor technologies, inspired by the biological olfactory systems of living organisms are emerging as a powerful tool for health diagnostics. These devices use sensor arrays to detect and analyze volatile organic compounds (VOCs) in breath or bodily fluids, enabling non-invasive, real-time detection of disease biomarkers. Their core functionality relies on sensing materials that transduce chemical signals into electrical data—materials such as chemiresistors, conductive polymers, optical sensors, surface acoustic wave devices, and electrochemical sensors. Advances in these materials open the door to portable, low-cost diagnostic tools capable of detecting early-stage illnesses, offering new opportunities in personalized and preventive healthcare.
Materials Class
Alloys (Oxides)
04
Technical Pitch
Technical Pitch
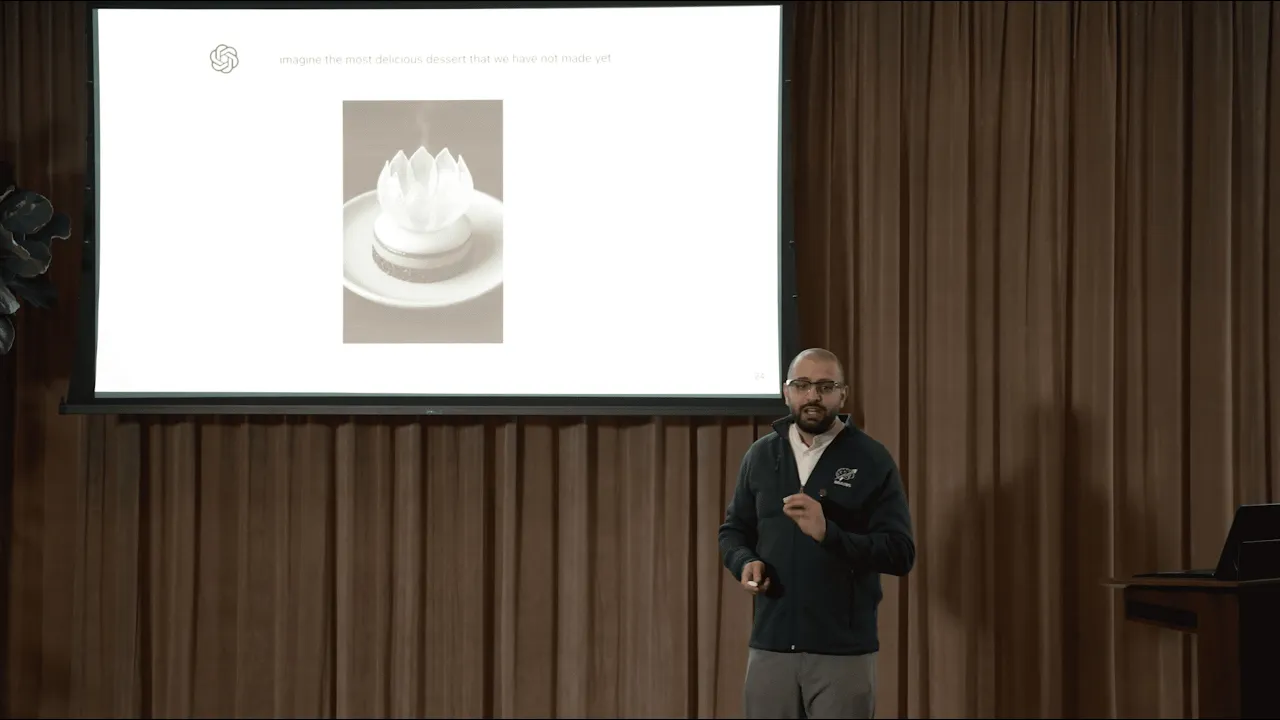
How (Our Approach)
How (Our Approach)
Thrust 1: Build Labs
Thrust 2: Scale Datasets
Thrust 3: Release Open Data
Self-driving labs and Miniaturized Chips
The Materials Data Factory will house and integrate multiple manufacturing equipment under one facility to streamline operations, eliminate delays, errors, and coordination challenges caused by multi-location setups. It will operate under precisely controlled conditions to produce high quality data reliably.
To make manufacturing data cheaper and faster, we will leverage self-driving labs that use continuous and real-time monitoring to operate with minimal human input. This will optimize manufacturing conditions faster through closed-loop feedback to increase hit rates—reducing material waste and experimental overhead. Additionally, we will use miniaturized devices (e.g., microfluidics reactors) to parallelize experiments and increase throughput.

Thrust 1: Build Labs
Thrust 2: Scale Datasets
Thrust 3: Release Open Data
Self-driving labs and Miniaturized Chips
The Materials Data Factory will house and integrate multiple manufacturing equipment under one facility to streamline operations, eliminate delays, errors, and coordination challenges caused by multi-location setups. It will operate under precisely controlled conditions to produce high quality data reliably.
To make manufacturing data cheaper and faster, we will leverage self-driving labs that use continuous and real-time monitoring to operate with minimal human input. This will optimize manufacturing conditions faster through closed-loop feedback to increase hit rates—reducing material waste and experimental overhead. Additionally, we will use miniaturized devices (e.g., microfluidics reactors) to parallelize experiments and increase throughput.

Thrust 1: Build Labs
Thrust 2: Scale Datasets
Thrust 3: Release Open Data
Self-driving labs and Miniaturized Chips
The Materials Data Factory will house and integrate multiple manufacturing equipment under one facility to streamline operations, eliminate delays, errors, and coordination challenges caused by multi-location setups. It will operate under precisely controlled conditions to produce high quality data reliably.
To make manufacturing data cheaper and faster, we will leverage self-driving labs that use continuous and real-time monitoring to operate with minimal human input. This will optimize manufacturing conditions faster through closed-loop feedback to increase hit rates—reducing material waste and experimental overhead. Additionally, we will use miniaturized devices (e.g., microfluidics reactors) to parallelize experiments and increase throughput.

Thrust 1: Build Labs
Thrust 2: Scale Datasets
Thrust 3: Release Open Data
Self-driving labs and Miniaturized Chips
The Materials Data Factory will house and integrate multiple manufacturing equipment under one facility to streamline operations, eliminate delays, errors, and coordination challenges caused by multi-location setups. It will operate under precisely controlled conditions to produce high quality data reliably.
To make manufacturing data cheaper and faster, we will leverage self-driving labs that use continuous and real-time monitoring to operate with minimal human input. This will optimize manufacturing conditions faster through closed-loop feedback to increase hit rates—reducing material waste and experimental overhead. Additionally, we will use miniaturized devices (e.g., microfluidics reactors) to parallelize experiments and increase throughput.

Thrust 1: Build Labs
Thrust 2: Scale Datasets
Thrust 3: Release Open Data
Self-driving labs and Miniaturized Chips
The Materials Data Factory will house and integrate multiple manufacturing equipment under one facility to streamline operations, eliminate delays, errors, and coordination challenges caused by multi-location setups. It will operate under precisely controlled conditions to produce high quality data reliably.
To make manufacturing data cheaper and faster, we will leverage self-driving labs that use continuous and real-time monitoring to operate with minimal human input. This will optimize manufacturing conditions faster through closed-loop feedback to increase hit rates—reducing material waste and experimental overhead. Additionally, we will use miniaturized devices (e.g., microfluidics reactors) to parallelize experiments and increase throughput.

Pilot Study
The feasibility of creating a large materials dataset was piloted by the Open Catalyst Experiments 2024 (OCx24) project. This effort was the result of 2+ years of development with Meta (FAIR Chemistry), University of Toronto and VSParticle.
The feasibility of creating a large materials dataset was piloted by the Open Catalyst Experiments 2024 (OCx24) project. This effort was the result of 2+ years of development with Meta (FAIR Chemistry), University of Toronto and VSParticle.
The feasibility of creating a large materials dataset was piloted by the Open Catalyst Experiments 2024 (OCx24) project. This effort was the result of 2+ years of development with Meta (FAIR Chemistry), University of Toronto and VSParticle.
Pilot Study
The feasibility of creating a large materials dataset was piloted by the Open Catalyst Experiments 2024 (OCx24) project. This effort was the result of 2+ years of development with Meta (FAIR Chemistry), University of Toronto and VSParticle.
Pilot Study
The feasibility of creating a large materials dataset was piloted by the Open Catalyst Experiments 2024 (OCx24) project. This effort was the result of 2+ years of development with Meta (FAIR Chemistry), University of Toronto and VSParticle.
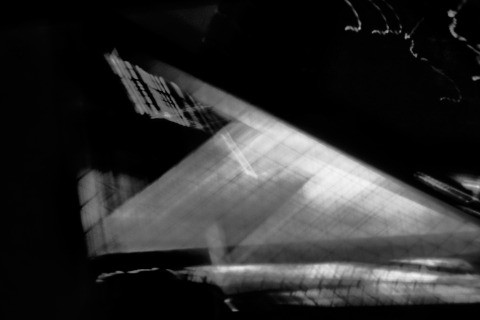
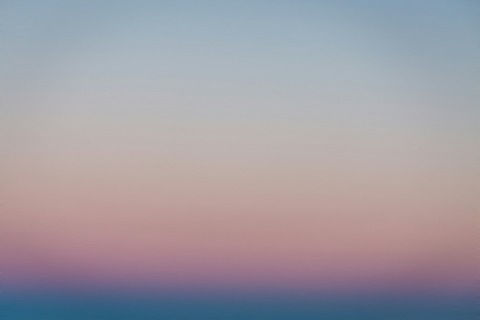
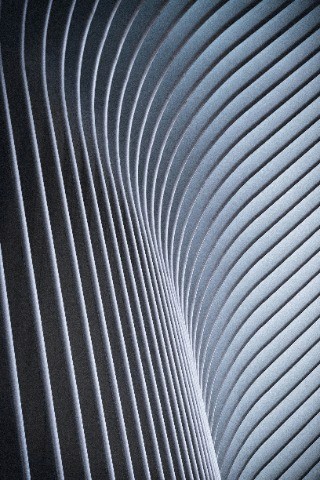
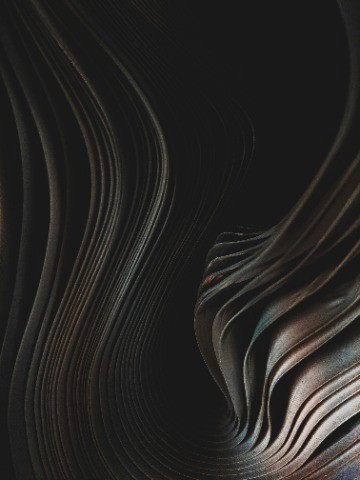
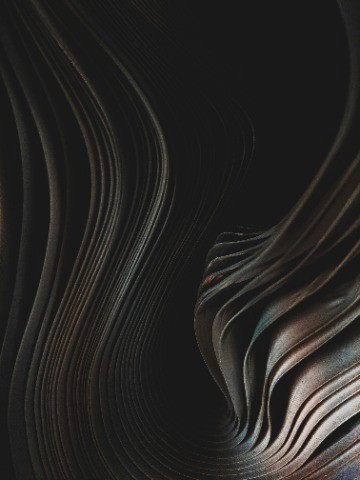
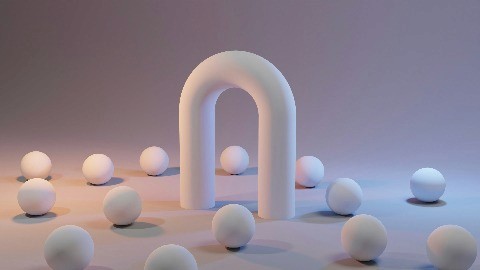

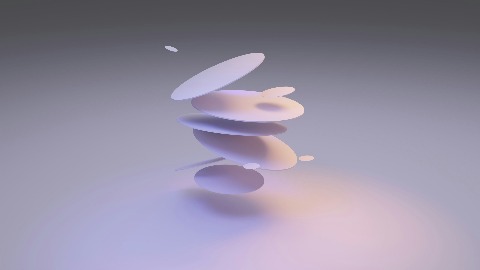